The Vital Role of Seals in Hydraulic Cylinder Manufacturing
In the world of industrial machinery, hydraulic cylinders play an indispensable role. These powerful devices convert hydraulic pressure into linear force, driving a wide range of operations from heavy construction equipment to manufacturing processes. Central to the efficient functioning of hydraulic cylinders are seals - seemingly small components that have a significant impact on overall performance and durability.
Hydraulic cylinder factories, scattered globally, understand the critical nature of seals. They are the unseen heroes that prevent fluid leakage, maintain system pressure, and ensure smooth, reliable operation. A hydraulic cylinder without a proper seal is akin to a leaky faucet, rendering the entire mechanism ineffective.
Seals are typically made from materials like rubber, polyurethane, or PTFE (Teflon), chosen for their resistance to wear, compatibility with various fluids, and ability to withstand extreme temperatures. The most common types include rod seals, piston seals, wiper seals, and buffer seals, each serving a distinct purpose. Rod seals prevent fluid from escaping around the moving rod, while piston seals stop fluid from passing between the cylinder barrel and the piston. Wiper seals, also known as scraper seals, keep contaminants out, and buffer seals mitigate the impact of sudden pressure surges.
The manufacturing process in hydraulic cylinder factories is meticulous, with engineers designing seals to precise specifications. The choice of material, shape, and hardness depends on factors such as the cylinder's operating conditions, the type of fluid used, and the level of pressure it will handle The choice of material, shape, and hardness depends on factors such as the cylinder's operating conditions, the type of fluid used, and the level of pressure it will handle
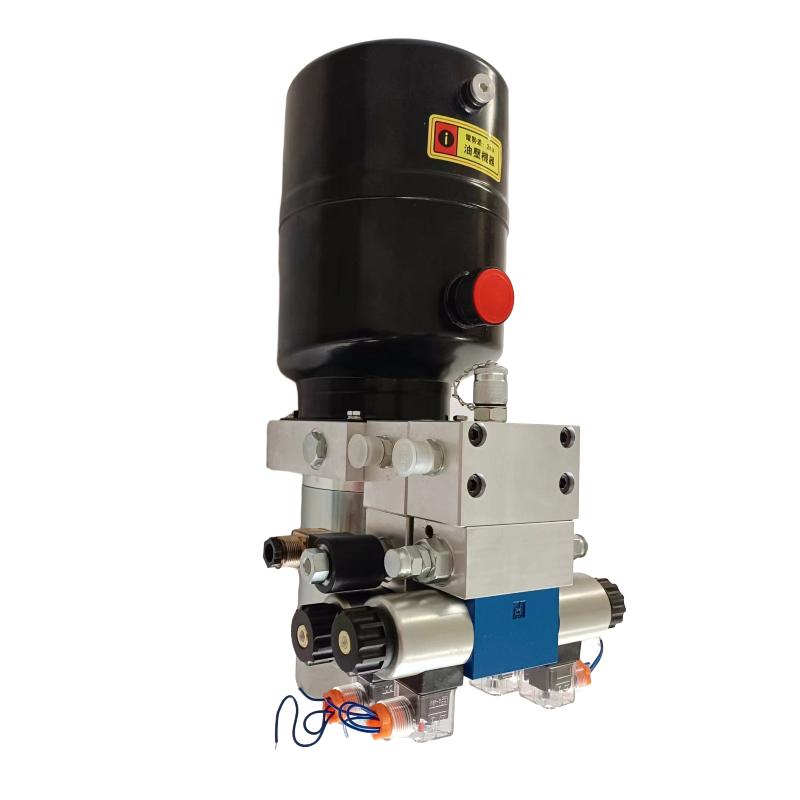
The choice of material, shape, and hardness depends on factors such as the cylinder's operating conditions, the type of fluid used, and the level of pressure it will handle The choice of material, shape, and hardness depends on factors such as the cylinder's operating conditions, the type of fluid used, and the level of pressure it will handle
seals in hydraulic cylinder factories. The design phase involves rigorous testing, simulation, and analysis to ensure optimal performance and longevity.
In the assembly stage, seals are carefully installed to prevent damage and ensure proper seating. Quality control is stringent, with thorough inspections conducted to verify the integrity of the seals before the cylinder is dispatched. Even a minor defect can lead to leaks, reduced efficiency, or even complete failure, highlighting the importance of precision in this step.
Moreover, regular maintenance and timely seal replacement are crucial in hydraulic cylinder factories. Over time, seals can wear out due to friction, heat, or exposure to harsh chemicals, necessitating replacement to maintain the cylinder's efficiency and safety.
In conclusion, seals in hydraulic cylinder factories are more than just components; they are the backbone of the system's functionality. Their role, though often overlooked, is pivotal in ensuring the smooth operation, reliability, and longevity of hydraulic cylinders. As technology advances, so does the sophistication of seal design, further enhancing the performance of these essential industrial workhorses. Understanding and appreciating the significance of seals is vital for both manufacturers and users of hydraulic cylinders alike.